Details about Industrial IoT tracks on June 30 at IIoT World Days 2020
June 30, 11:15 - 12:15 AM ET
Maximizing Business Resilience through Digital Services
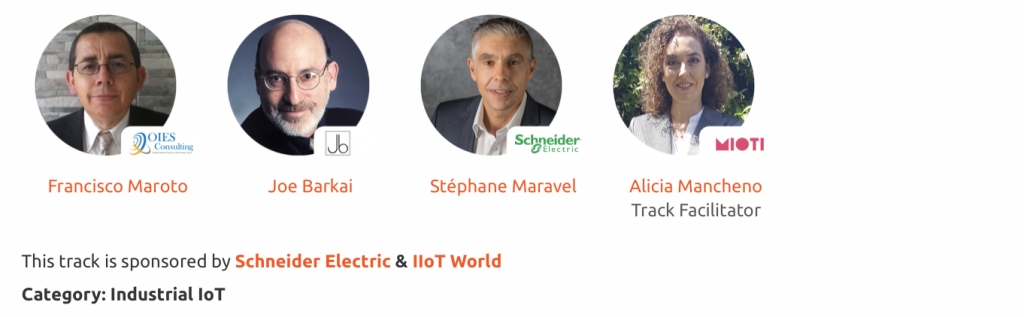
Is it possible to democratize IIoT technologies?
Topics to be discussed and questions to be answered during this presentation:- Could the democratization of IIOT technologies improve the competitiveness of SMBs?
- What are the top challenges of Industrial IoT SMBs?
- What are the top challenges of Industrial IoT Startups?
- What should be the role of local, regional, national or EU Governments do accelerate adoption of IIOT in SMBs?
- Collaboration or Competition with the Tech / Industrial Giants?
The Outcome Economy: How the Industrial Internet of Things is Changing Every Business
Maximizing Business and Operational Resilience through Digital Services
Key takeaways:
- Learn what tactical steps you can take to improve your organization’s continuity plans
- Understand what business challenges your peers are prioritizing and how they plan to manage them with digital services
- Hear how your peers have used digital services to optimize processes and operations and ensure business resiliency
June 30, 12:20 - 1:40 PM ET
Artificial Intelligence – how manufacturers address this disruptive force in 2020
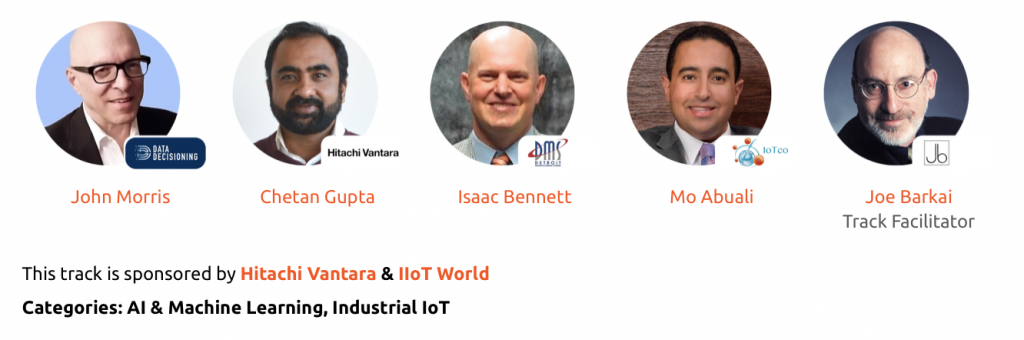
Nine Ways Business-Side Managers Can Lead A Successful AI Program For Business Transformation
- FOCUS ON DECISION-MAKING – The business case for big data, AI and other technologies is justified on better decision-making, especially examining questions of uncertainty, risk and decision frequencies.
- GUIDE BIG DATA PROGRAM – The only business meaning of “big data” is “too big for our systems” – and this means that we have to throw away a lot of our data. This concerns business policy.
- INVEST HARD-WON KNOWLEDGE – Any automation program will be enormously dependent on human knowledge for success, typically earned from years of human experience.
- TAKE RESPONSIBILITY FOR MODELS – Whether digital twins for machines, deployed AIs, or for fullon business system simulations, the executive must “open up the black box”. There is no competitive edge or legal protection in giving up responsibility to a black box.
- ENSURE NOT TO DROWN USERS – The economic principle is “data is cheap and business analysis is expensive”, and the inevitable temptation is to add ever more data outputs on some system. As a result alarm fatigue and information overload in healthcare, transportation, oil exploration etc. is endemic.
- STRATEGY OF AUGMENTATION – The work of business will not be automated away. The recipe for automation success is augmentation, not substitution.
- FOCUS ON DATA STANDARDS – As decision oriented management technology begins to permeate an organization, the requirement for high-quality data becomes more pressing. New data governance commitments are required.
- REALIZE IT IS MANUFACTURING – The idea of “automation artefact manufacturing” is new for many organizations. But a big data program or an AI program is not a one-off. It is a commitment to a production cycle of new management tools.
- LEAD FROM STRATEGY – The question of overall strategy is outside the scope of this presentation.
Artificial Intelligence in Manufacturing: Case Studies on Predictive Maintenance and Predictive Quality
- Address many of those challenges and present compelling real-world business examples with demonstrated value for rapidly deploying AI in manufacturing.
- Introduce a methodology including a workshop to define the business and technical problem, a state of the art and end-to-end analysis platform from data collection to the delivery of the health and process information, and lessons learned on how the solution can be maintained and improved over time.
- Present real world manufacturing examples with ROI including stamping, casting, CNC machining, industrial robotics, among others. Examples in predictive maintenance that focus on reducing unplanned downtime will be shared along with case studies on predictive quality, in which the theme is improving quality and reducing scrap.
June 30, 3:05 - 4:00 PM ET
[Panel Discussion] Where to start with IIoT and the true cost of integrating IIoT into your business
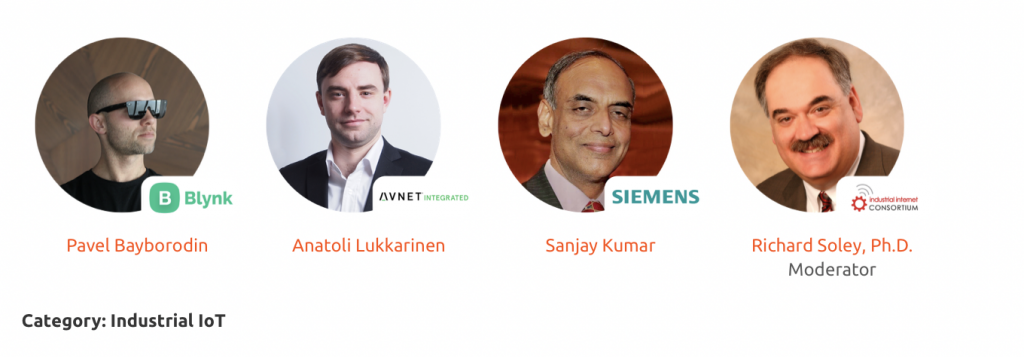
This panel will cover (amongst many things):
- Where to start with IIoT
- A breakdown of costs when integrating IoT into business processes and products
- Why hardware has a critical role in successful IIoT solution
- How product lifecycle affects your profitability
Check the speakers here.
June 30, 4:05 - 5:40 PM ET
The Manufacturing Analytics Journey
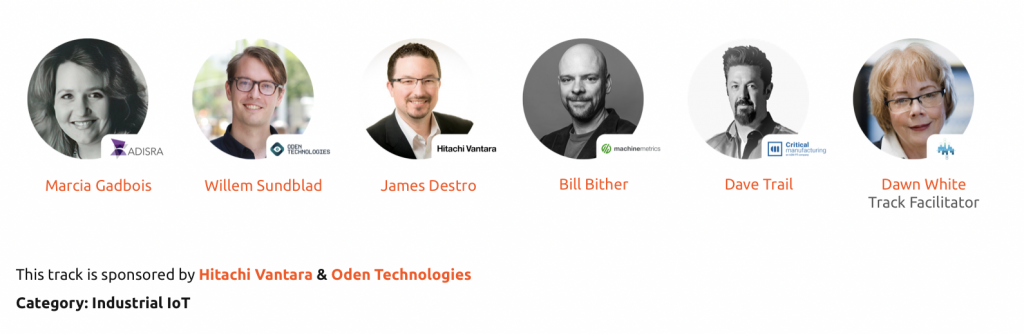
Evolution of Predictive Maintenance
How To Improve Profitability With Advanced Analytics
The Intelligent Manufacturing Journey
Where/when to invest time and resources to drive continuous value
- Discover how to identify where your organization lands within the Analytics Journey to help define what steps you can take to create immediate value
- Understand where/when to invest time and resources to drive continuous value
- Learn about the MachineMetrics secret sauce: a use-case driven technology roll-out plan we call “the hybrid platform”
Analytics and Big Data, and how it underscores Industry 4.0
Resources to download
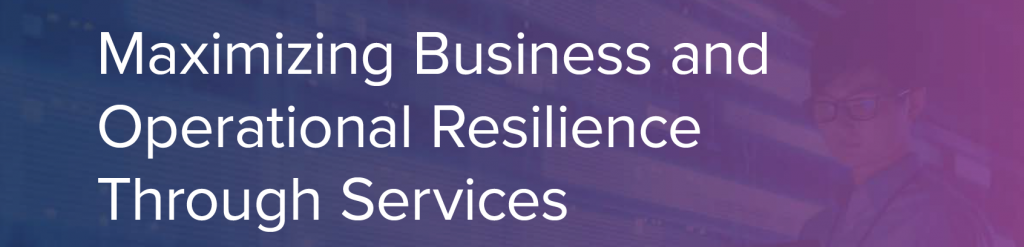
A white paper by IDC, sponsored by Schneider Electric
Download the Maximizing Business and Operational Resilience Through Serviceswhite paper to learn how global companies see the challenges and opportunities of digital transformation, and how third-party services help pave the way to success.
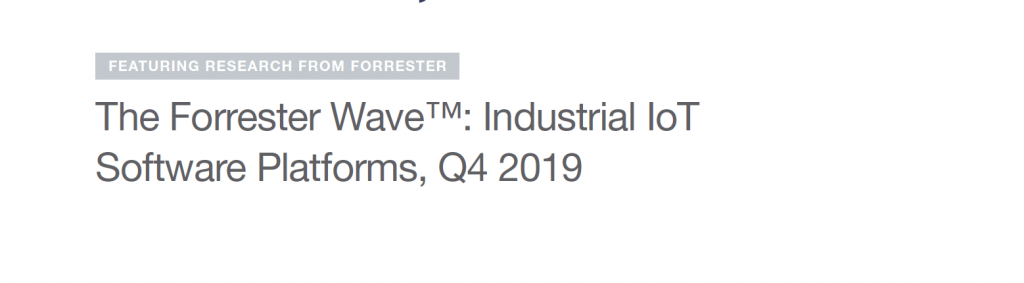
In The Forrester Wave™: Industrial IoT Software Platforms, Q4 2019, a 24-criterion evaluation of industrial internet of things (IIoT) software platform providers, the research company identified the 14 most significant — ABB, Amazon Web Services (AWS), Bosch, C3.ai, GE Digital, Hitachi, IBM, Microsoft, Oracle, PTC, Samsung SDS, SAP, Siemens, and Software AG — and researched, analyzed, and scored them. This report shows how each provider measures up and helps infrastructure and operations (I&O) professionals select the right ones for their needs.
This report is sponsored by Siemens.
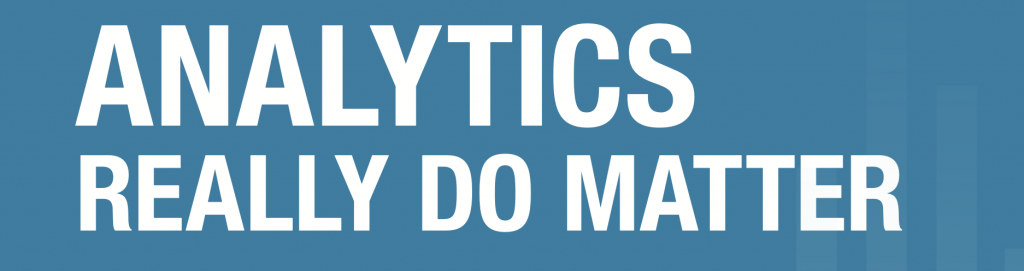
This e-book sponsored by Hitachi Vantara introduces:
- The results of the 2018 Analytics that Matter survey and the unexpected (and interesting) responses; and
- A data and analytics architecture that fits within the Operational Architecture prescribed by LNS Research and that helps manufacturers achieve Digital Transformation goals.